With a Mora knife I carve the entry point up at the heel end. I don’t have to make an exit point since there’s no head on these ukes. The walnut cuts like butter as long as the knife is sharp and the edge is of the scandigrind variety.

There’s a lot of end grain going on up by the body but it’s no problem. One thing I do recommend is clamping whatever you’re carving securely to the bench.

Then a few spokeshaves of different sizes make short work of shaping the neck. It takes about ten minutes but I wouldn’t mind an hour - this is my favourite task.
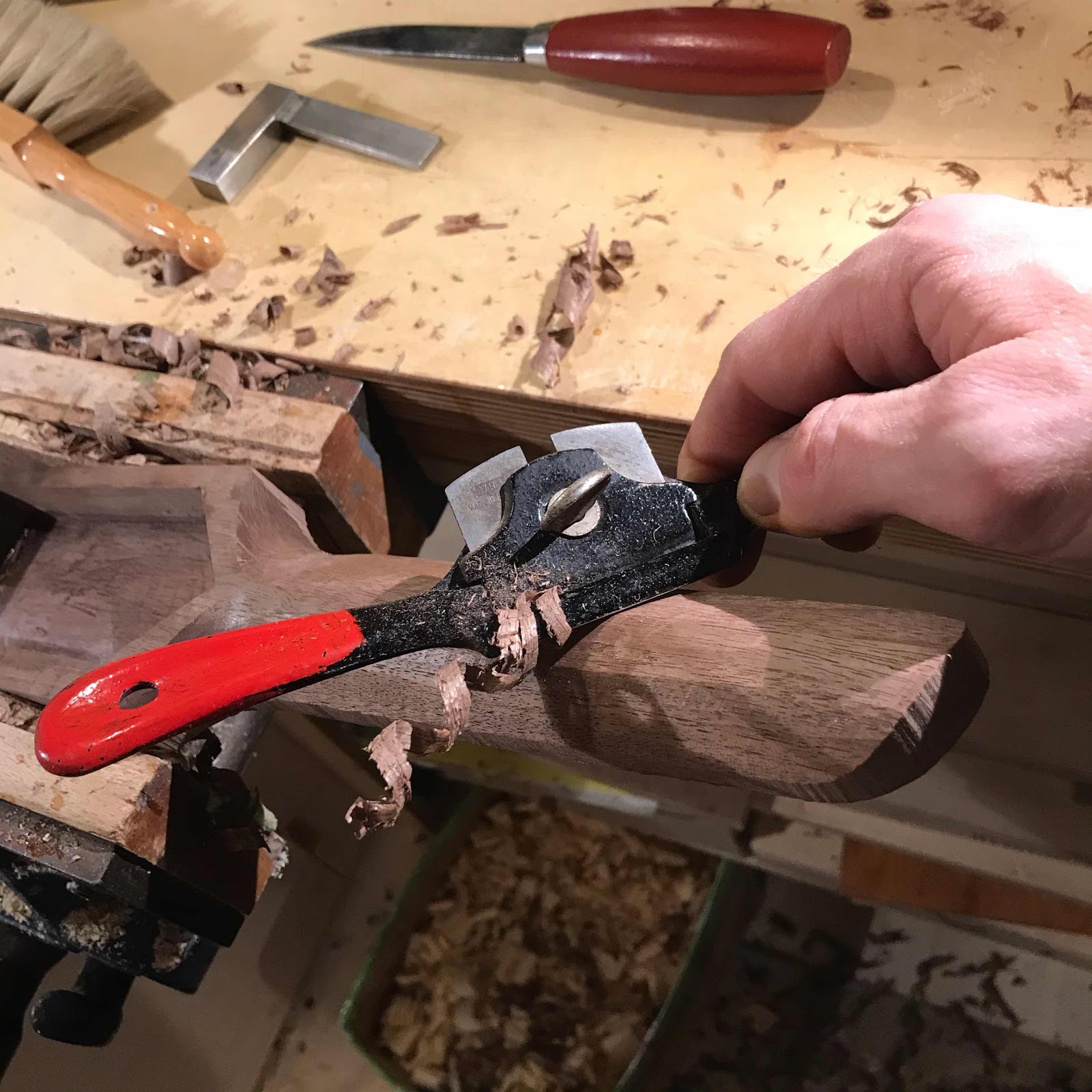
And I got to use my new fret slotting jig. The old one was a bit worn out and the first replacement I made turned out wonky. Which is really bad when it comes to a jig. For positioning frets.
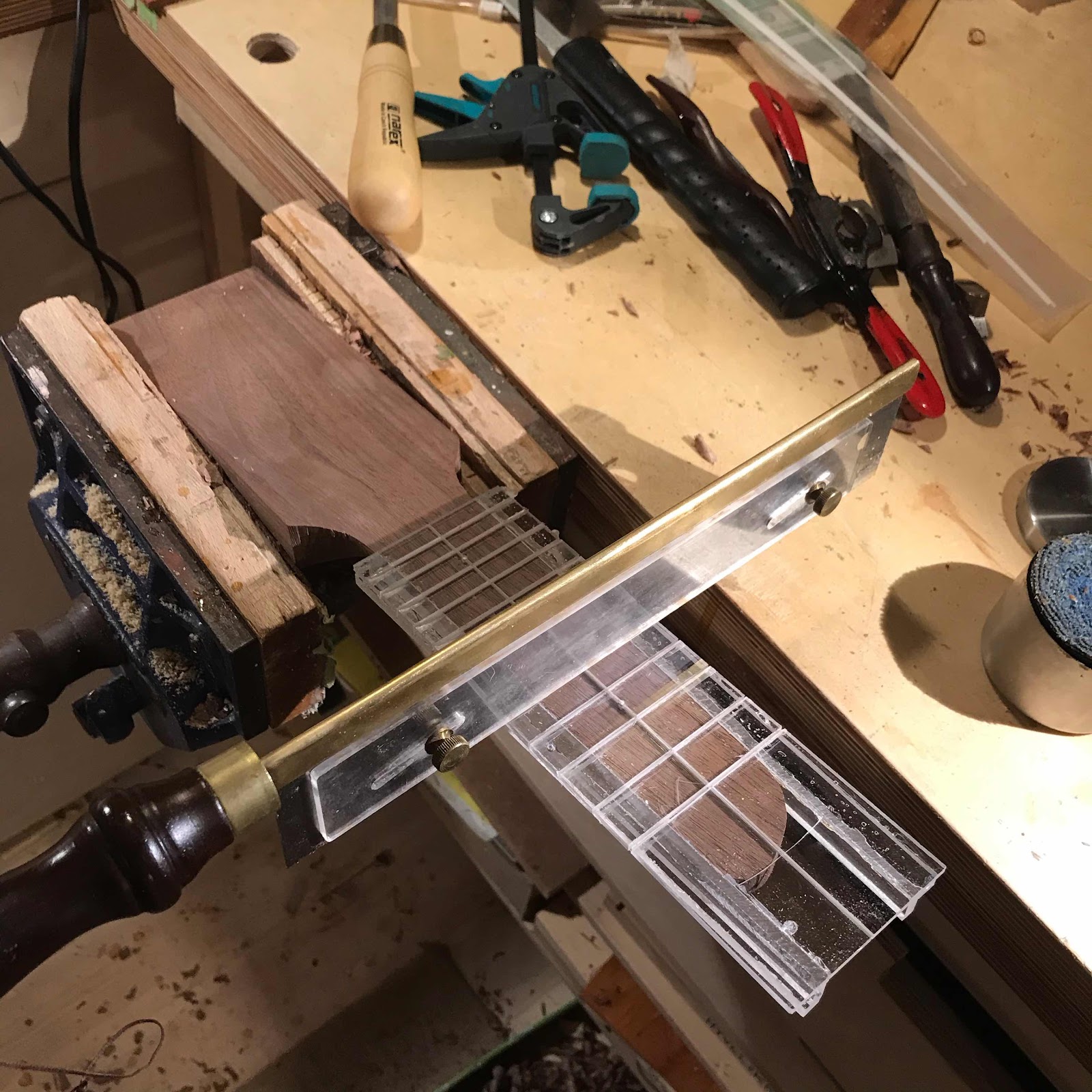
There’s a lot of end grain going on up by the body but it’s no problem. One thing I do recommend is clamping whatever you’re carving securely to the bench.
Then a few spokeshaves of different sizes make short work of shaping the neck. It takes about ten minutes but I wouldn’t mind an hour - this is my favourite task.
And I got to use my new fret slotting jig. The old one was a bit worn out and the first replacement I made turned out wonky. Which is really bad when it comes to a jig. For positioning frets.