I’m back (I never left)! It’s been hell at the day prison thd last months, and it still is. But I have cleaned up the workshop [a bit] and tonight I was back at it.
The plates I sanded a while back will give me two mahogany sopranos and two cherry piccolos, if I don’t mess up. I picked through the wee pile and marked out the contours. I got lucky with the grain direction in the mahogany piece - the heelcaps tucked in side by side so the length was enough for all four plates.

Maybe it’s visible in the middle there. The heelcaps. Wot I wrote.

But before I get to start I need to finish this one - the half built soprano I’m making for a friend. It isn’t all that much left. I strapped it into the workboard and started on some back braces.
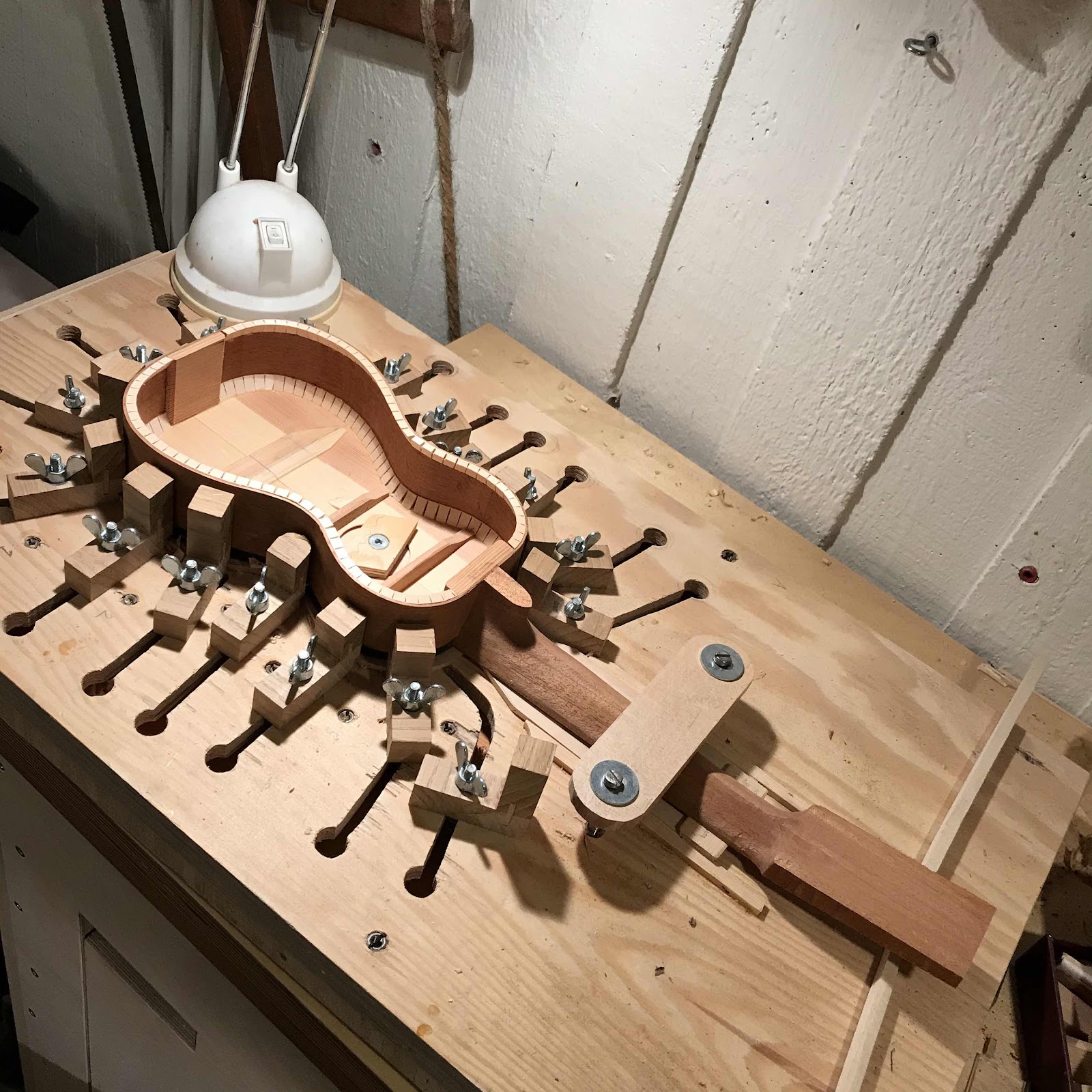
A very light and straight piece of spruce that I found somewhere will do nicely. I split it with my something something knife.

Then I ripped the split off piece with my cute rip saw. Maybe the knife could’ve done this as well but no chances were taken. And ripping is fun.

I’ll leave you with this image to haunt your dreams - a no. 3 Stanley plane and the Stewmac nut vise. I get the profile first before I cut it to length and curve the wide edge for the back arch.

I’ll try to be quicker with the updates. Fanx for staying tuned to this ancient blog.